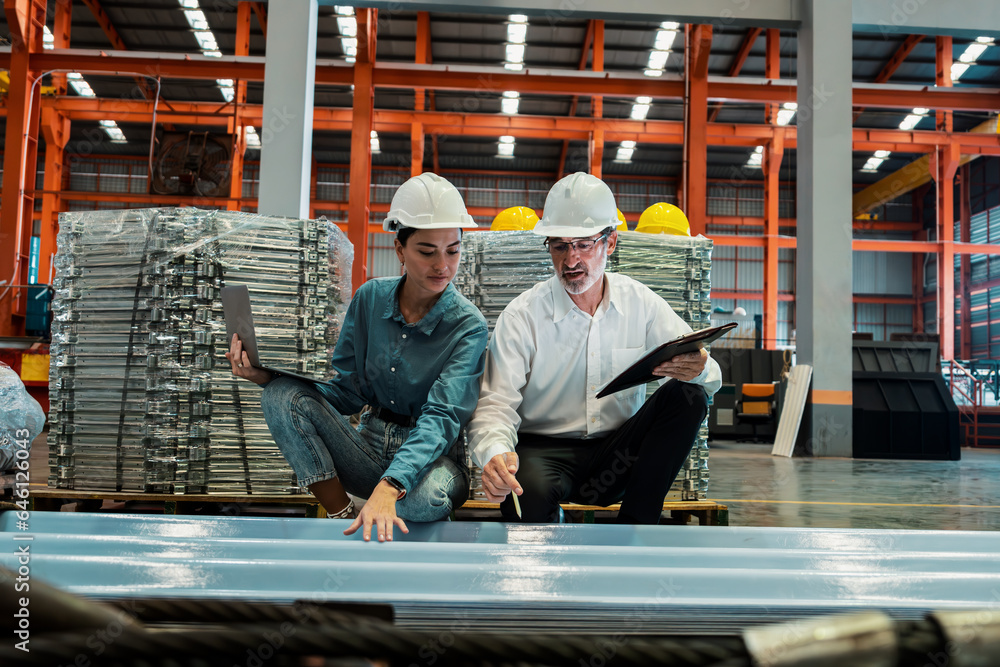
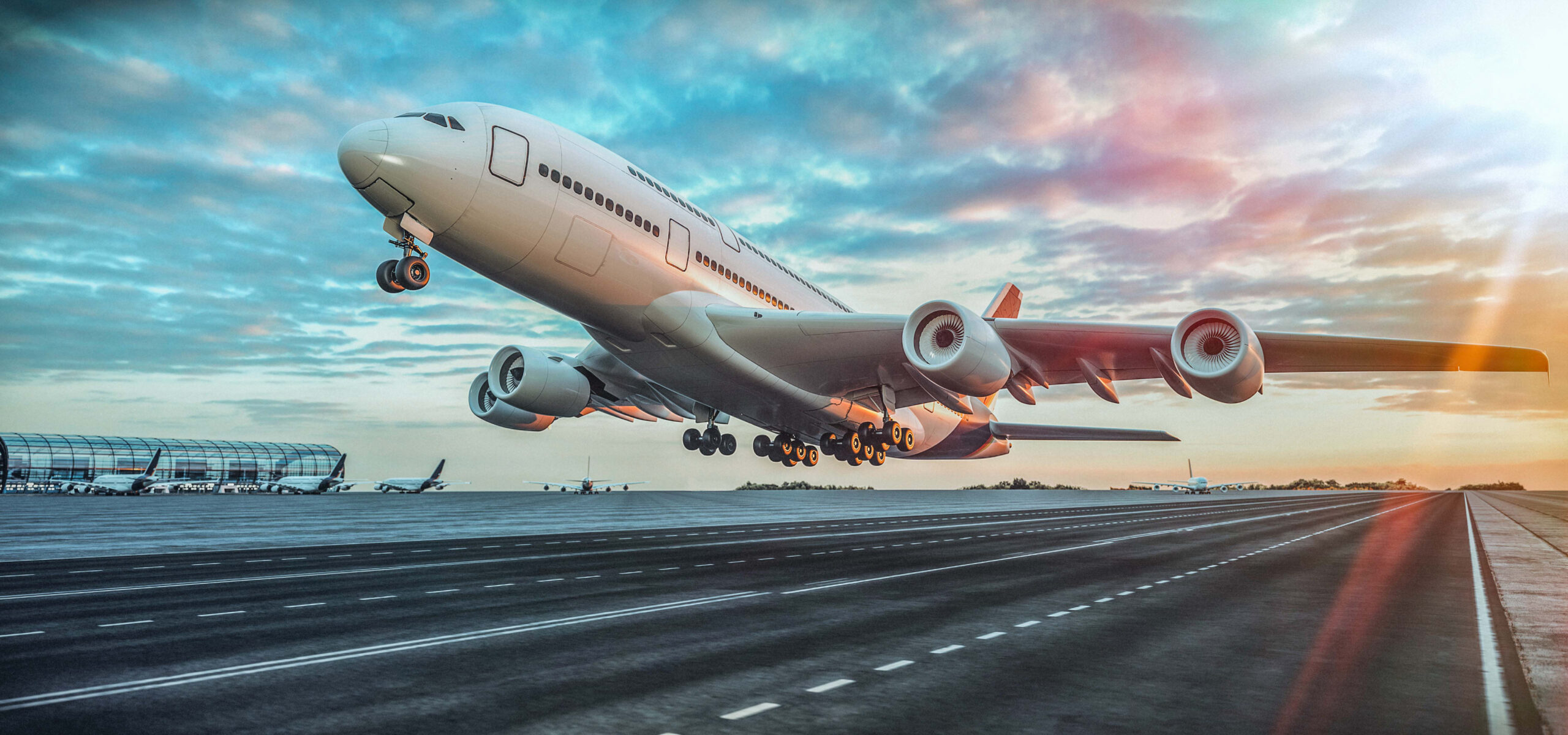
Composite materials are a key aspect of the aviation sector, giving engineers the ability to deal with a variety of different obstacles that they would face if they were trying to use certain materials in an individual manner. Composite materials are simply the process of combining at least two different materials.
Each of the materials still has their own identities when they come together in the composites, they will not merge entirely into one another and will not dissolve. As a result of this relationship, a hybrid type of material will be the end result, which allows for a lot of enhanced structural attributes.
Composite materials in aviation tend to be pretty lightweight, resistant to high temperatures, and are ideal for all forms of high performance. Over time, the deployment of these types of materials helps to lower consumption of fuel, increase efficiency, and lower the overall direct aircraft operating costs.
Over the years, there have been numerous notable uses of composite materials, with some standout Boeing aircraft, in particular, utilizing plenty of composite materials for various purposes.
One of the all-consuming aspects of manufacturers and engineers in the aviation sector is constantly striving to improve the overall performance of their aircraft, whether these are military or commercial planes. As a result, there is constant experimentation and development of different types of structural materials.
Composite materials are a key part of this process, allowing for the ongoing development of improved components. The reason why these types of materials are particularly of massive value in the aviation sector is that they tend to be extremely strong while still having optimal stiffness to density ratios, and improved physical properties.
For many years, the process of constructing commercial aircraft and its materials has not deviated too much. One of the keys to this success is the durable and tough sheet metal that is used for a large portion of the development. However, there are certain types of limits that the use of sheet metal will have. Composite materials will be able to supplement or even replace sheet metal in certain aspects of the construction process.
The origins of using composite materials as part of the development process of aircraft date back to around 1951 in Europe. In West Germany, the design and production of the Akaflieg Stuttgart FS-24 caused a lot of fiberglass material. A composite of glass fiber and balsa was used as part of its construction, as opposed to the fiberglass, foam, and epoxy resin that is used in aircraft these days.
Balsa is a material that is extremely light and very easily manipulated into all forms of shapes However, it is very fragile and does not have much tensile strength. Therefore, glass fiber was sandwiched with the balsa in order to add plenty of strength to the surfaces. Finally, aircraft standard plywood was then used in order to strengthen the points that would be bearing loads.
Many manufacturers in Germany continued to prefer the use of fiberglass in the construction process thereafter for a number of decades. A young engineer in the 1970s named Burt Rutan began the movement of the significant use of composite materials through the design and production of aircraft.
The first aircraft that started taking this approach were generally small, high-performance planes. Foam began to be used as a part of the process as it is the most malleable type of material you will be able to use for designing aircraft. This is because you are able to carve, cut, and shape it in any type of way that you prefer.
As time went on, modern mainstream aircraft manufacturers began to look at the use of composite materials. One of the biggest mainstream planes that extremely utilizes composite materials is the Boeing 787 Dreamliner. About half of the design of this plane was through the use of composite materials. In particular, these materials are especially a key component of the empennage, wings, and fuselage.
For jets that are relatively heavy, the main advantage of utilizing composite materials is the savings that there will be through reducing the overall weight of the aircraft. The more that a plane weighs, the more fuel that will then be consumed. Therefore, the duration availability is going to be lengthier and more passengers or cargo can then be accommodated, leading to lower cost for operating.
According to Boeing estimates, the use of composite materials in key aspects of an aircraft will lead to the weight being 20% lower than if metal structures were used. This research also highlights that when structures are using composite materials that there will be much less maintenance necessary than if these structures were using comparable aluminum. While the Boeing 777 tail is made out of composite materials and is 25% bigger than the B767 aluminum tail, the former needs 35% fewer worker maintenance hours.
As mentioned, there are a number of different advantages that are associated with using composite materials when constructing aircraft. These are all different things that need to be considered by engineers and designers of aircraft.
They can decide for themselves if composite materials are the most appropriate form of materials to be used in certain situations. Here are some of the key advantages associated with composite materials in aviation:
Composite materials are very strong, particularly when they are compared to the likes of aluminum and steel. Composite materials also have the advantage of being much more easily crafted into specific designs. As they are both lightweight and have plenty of strength, composite materials will possess one of the best strength-to-weight ratios when it comes to different materials.
If parts of an aircraft need to be stronger in certain directions, composite materials can be used in a more efficient manner. Otherwise, thicker materials will be needed if using alternative materials increasing weight. Composite materials will be strong in any direction you want without adding this extra weight.
Composite materials have the ability to withstand a lot of potential moisture damage, as well as chemical corrosion from acid rain that would be an issue for the likes of alternative metals. Therefore, this will decrease the amount of maintenance and replacements that will be needed through these various types of damage, resulting in lower costs.
As composite materials have the ability to mold into many different complicated shapes without having to utilize any high-pressure tools, they have a lot of aviation-related uses.
Composite parts can be designed in such a way that they are stronger in a certain direction and will be resident to bending. Traditionally, multi-unit parts can often be replaced by composite materials which will streamline down the assembly process.
As composite materials are not going to be good conductors of electricity and heat, they will be an ideal way to insulate important parts. If there is a circumstance where it is important that there are parts that are thermally conductive, these types of materials can be merged into the composite component as needed.
With the world becoming a lot more focused on green solutions and reducing environmental impact, aircraft design is playing a key role in this space. Thanks to the lighter weight of composite materials, there will be less of an environmental load. The composite materials parts will normally last longer than metal alternatives as they are going to be more resistant to corrosion.
More and more engineers are starting to use composite materials that are biodegradable through the use of natural fires. These will still carry the useful characteristics of normal composite materials while lessening the impact on the environment.
There is no doubt that composite materials are here to stay in the aviation sector. They have so many great attributes that they can be an asset in most types of aircraft if necessary. Engineers can decide how much composite materials are needed in a given build, but there will almost always be some shape or form that these materials that will come in handy.
As time goes on, composite materials are only going to become better as technology improves. New designs and types of materials will come to the fore and produce even further benefits. Manufacturers are happy to invest time and resources into the research and development as the use of composite materials can lead to significant savings in costs thanks to their lightweight nature and durability.
Some of the best manufacturers of composite materials in this day and age include the likes of Park Aerospace and The Gill Corp. They are two respected companies with many years worth of experience. These companies are committed to a wide variety of composite materials applications, for all sorts of different aircraft.